The advantages of working with Moon Build
Having worked as Bristol’s premier design & build business for the past 20 years, we recently concluded that there is an even better service model we can offer.
Separating the Design function from the Build gives you total flexibility, you are in control. You can either appoint Moon Design to produce all the design & technical information for your project and then work with any builder you choose, or if you like the idea of working with Moon Build you can engage them earlier in the process and take advantage of a more joined up approach.
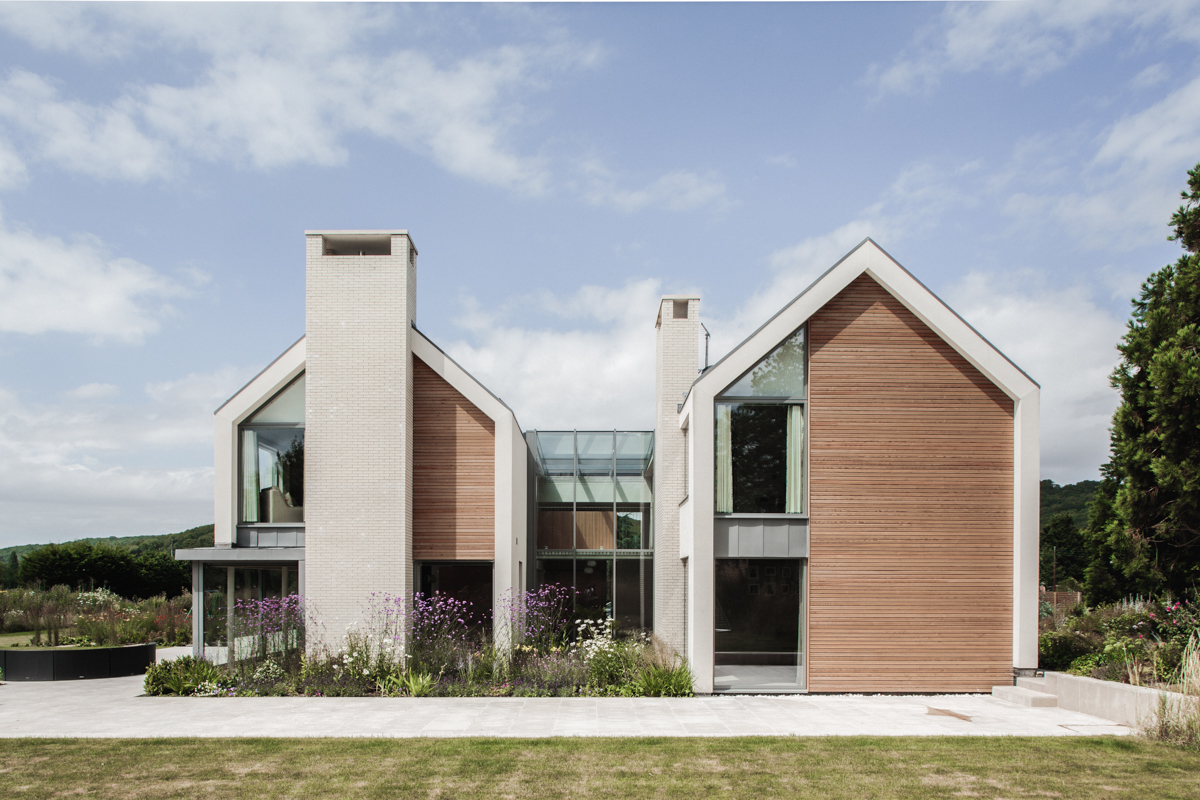
Why separate designer and builder?
We believe that independence between the designer and the builder is crucial for two reasons:
The first is that it establishes creative freedom. There is a big difference between someone simply producing the drawings required to build your project, and a truly creative process with an experienced designer working in a creative environment; exploring design options that are right for you.
The second reason is that it fosters a healthy conflict between the architect and the builder. The design solution should be about you and your aspirations, not just how to make the project easier to build for the advantage of the builder.
Understanding the budget earlier in the process
Once Moon Design have produced the concept designs, Moon Build can provide a Preliminary Budget based on these designs and your project brief. This will give you a good understanding of the overall budget and will help you and Moon Design to develop your scheme. You then have the option to appoint Moon Build on the basis of this budget.
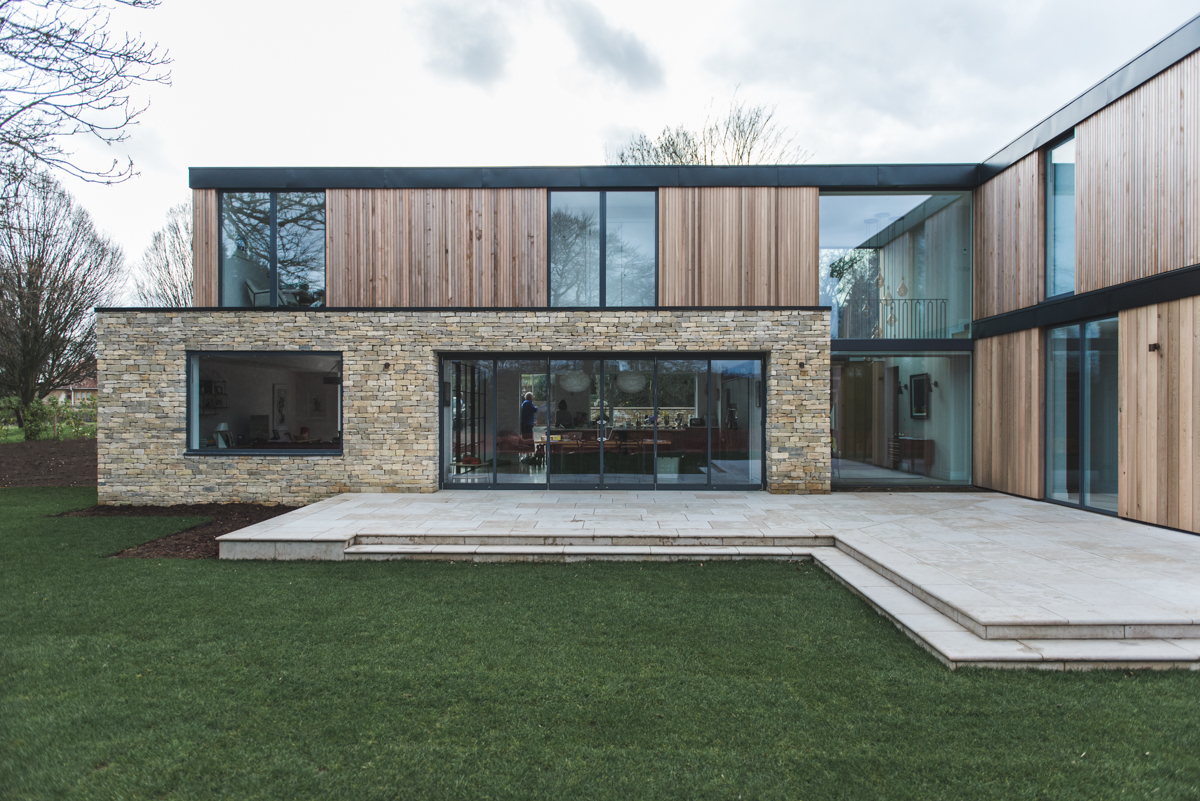
Timescales & Certainty
Appointing Moon Build at this earlier stage will reduce the timescales of the project considerably. It will give you more certainty of the site start date and provide you with the security of having a high quality contractor booked in. If you decide to go to a conventional tender, you will not be able to secure a slot in a contractor’s programme until you have accepted their tender return, adding as much as 12-18 weeks to the process.
A more joined up offering
If Moon Build are appointed earlier in the process, they can start to work with you during the Planning application period to help you to make choices regarding all of the interior fixtures and fittings, working to the overall design intent provided by Moon Design.
Appointing the same people to provide the internal fittings specification as those who will be delivering it on the ground creates a more efficient process, clarifies responsibility and you are able to take advantage of their knowledge and experience of delivering hundreds of projects similar to yours.
Moon Build are also able to provide a very cost-effective solution when supplying the fixtures & fittings, due to the discounts they have negotiated with their suppliers over the years.
We have worked together on over 400 projects; we are cut from the same cloth. They have a track record of delivering extremely high-quality projects and they understand design detailing and design intent. Moon Design will be available to answer any of their design queries during the build.
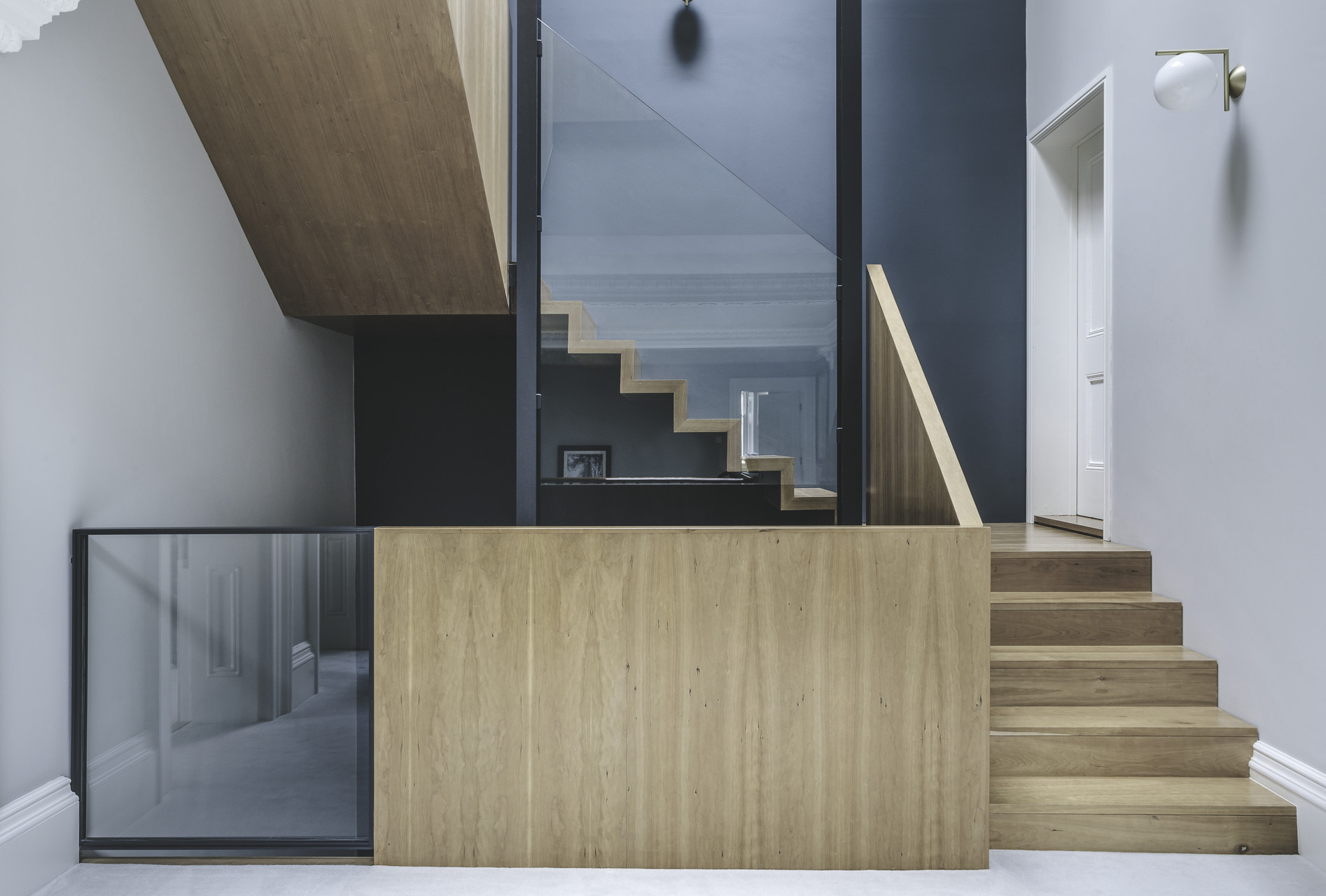
The Risk factor
As you can hopefully now see, the appointment of Moon Build earlier in the process provides a lot of advantages. However, as would be the case with any procurement route, appointing the contractor early in the process, before all of the project drawings and specifications have been prepared, creates a level of uncertainty around the final budget. Any contractor will have a hard time providing a 100% accurate price without all of the project information in front of them.
Our joined up approach seeks to minimise this risk, by ensuring that concept level drawings prepared by Moon Design are rooted in the reality of having delivered over 400 projects across the whole property spectrum. This enables Moon Build to deliver a more reliable Preliminary Budget and reduce cost surprises further down the line.
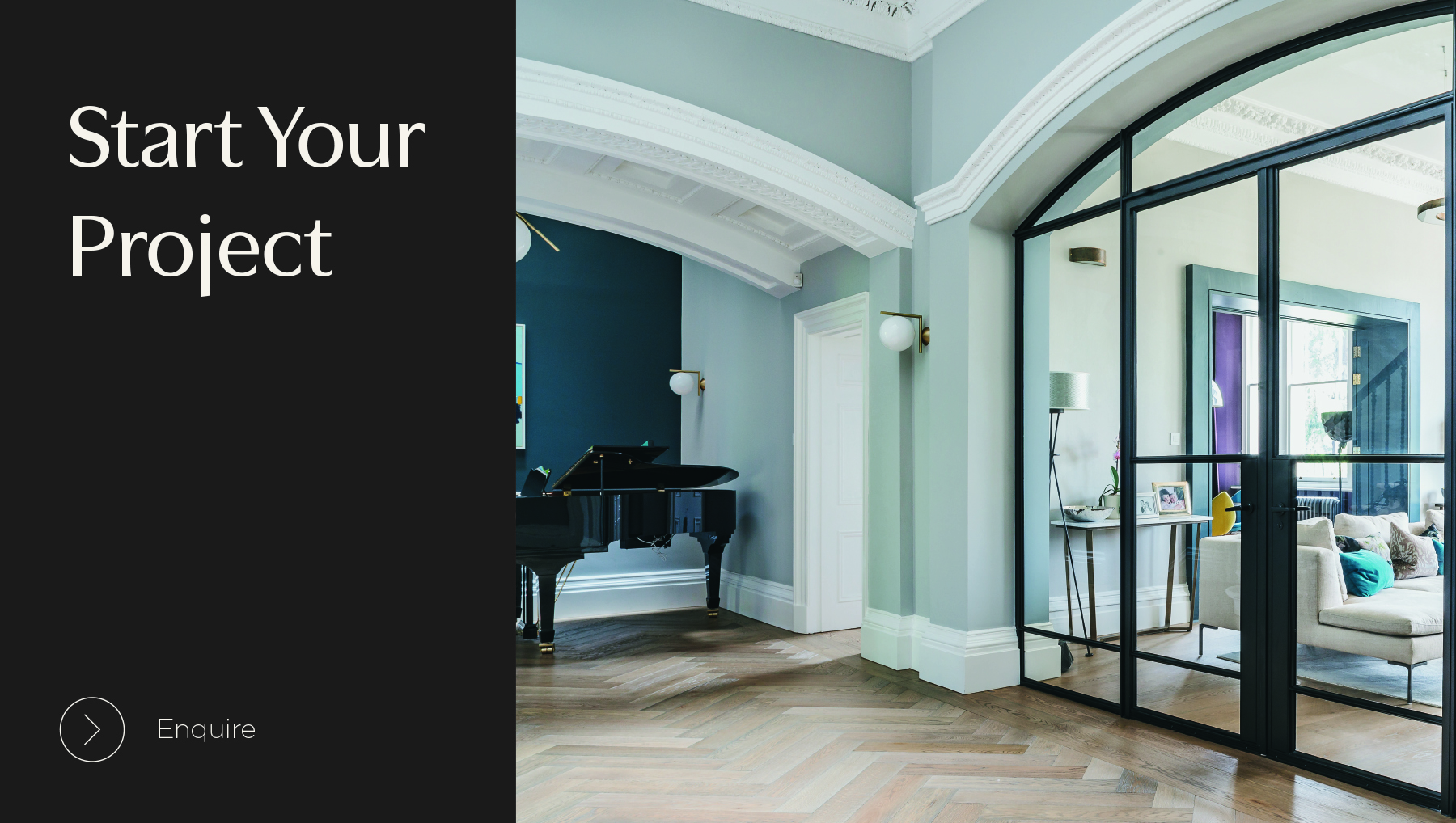